Background of caliper development
The original brand "GALE SPEED", which was launched by Active in 2002, is responsible for the comprehensive customization of the suspension. We have released forged wheels, brake discs, and master cylinders, but we still needed calipers to maximize the braking performance we pursued with them.
Therefore, the active and first caliper development started from scratch as "a project to make GALE SPEED's dream come true".
|
|
1. Concept decision-design design- What is the caliper produced by GALE SPEED?
|
|
The concept started with the developer's desire to "make amazing things that are not in the world."
The elements required for calipers are rigidity, durability, lightness, coolness, etc.
As long as I have decided to do it, I want to aim for the best. Therefore, we examined the advantages and disadvantages of each of the 1-piece and 2-piece caliper structures, and finally combined the advantages of the 2-piece structure with the 3D cutting technology of GALE SPEED's highest peak series Elaborate. I decided to make it. |
|
Image diagram
|
|
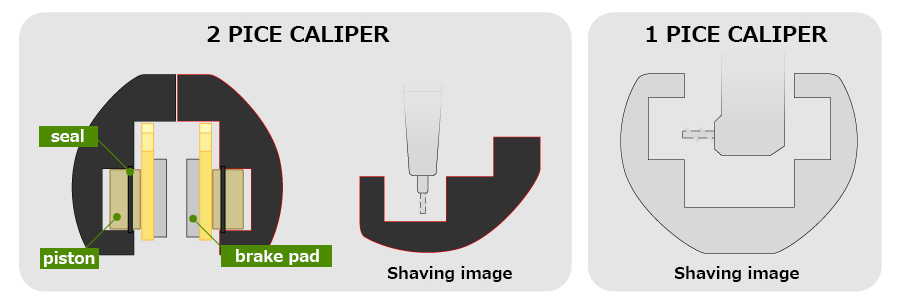
|
|
Features of 2-piece caliper |
Merit |
There are few restrictions on processing tools, and the body can be cut compactly.
|
Demerit |
The rigidity of the caliper body is lower than that of the one-piece structure. |
Small piston discharge
(less deflection during braking) |
It tends to be heavy because it is fixed with bolts. |
|
|
|
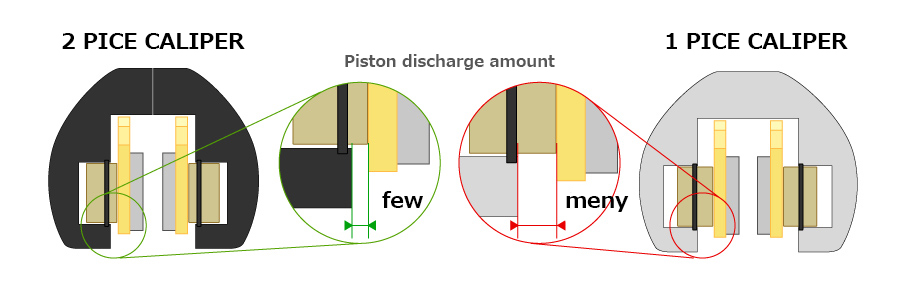
|
Image of piston discharge amount
|
|
|
2. Prototype of the first machine-Test Completion of the long-sought prototype |
|
At the 2014 Tokyo Motorcycle Show, we exhibited a half-cut aluminum block, and for the first time expressed our intention to "make calipers" externally.
From that point on, design and prototyping began in earnest, but since the machining center capable of 5-axis machining constantly mass-produces Elaborate master cylinders, it was difficult to schedule normal production and caliper prototyping.
We had the knowledge and know-how cultivated in the design and manufacture of master cylinders, but the calipers also required completely different processing technology and knowledge. When the first caliper made by trial and error while compensating for it was put on a brake test bench (a test machine that can specify conditions such as vehicle weight, vehicle speed, deceleration, pad temperature), it became a general brake. I was very impressed that it worked as well!
|
|
3. Brushing up the specifications Aiming for height |
|
At the same time as I was able to make one prototype, I also wanted to improve it. |
|
1. |
How can I get rigidity with a two-piece structure? This (in the case of front 4P) was able to have rigidity at the time of braking by using four fastening bolts and providing a center bridge. |
|
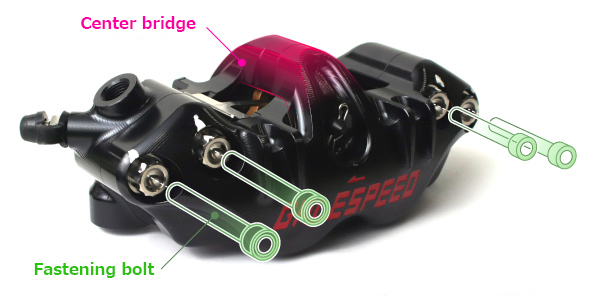
|
|
2. |
Tested by changing the groove size of the piston seal to various sizes in order to smooth the movement of the piston and obtain an appropriate piston back amount. |
|
3. |
The caliper body has the problem of insufficient heat capacity if it is made lightweight and compact, but I want to keep it as small as possible. Therefore, the idea of attaching the "fins" that became the feature of the GALE SPEED caliper came out. It is a method to increase the heat dissipation effect instead of increasing the heat capacity. As the test progressed, the fins became larger, and when combined with a 3D cutting body that originally had a large surface area, it showed a high cooling effect. It is finished in a processed finish that has both beauty and performance. |
|
|
4. Durability test Commitment to reliable quality |
|
I turned the brake test bench (testing machine) countless times to check the durability. We collected data in various patterns, but we conducted a lot of tests in which the vehicle weight of 300 kg was repeated from 200 km / h to full braking until the fluid exceeded the boiling point under the conditions at the time of comparison. You can also grasp the limit by conducting the test in an environment that is harsher than the actual driving conditions. After repeating the full brake test many times, the brake disc got hotter and more, and to my surprise, my arms and face were tanned and turned black.
The prototype that passed the bench test was mounted on the vehicle to check the operability, brake feeling, and other parts that can only be understood by human sensibilities, and was tested by a professional rider. We tried compatibility with various discs and pads, and made the specifications target from normal driving to sports driving.
There were some regrets that were unpopular at the beginning of the test drive in the company, but in the end it was a great pleasure to be able to get a satisfactory evaluation. |
|
5. Mass production specifications confirmed Finally to be released |
|
From the data accumulated over many years, we decided on the one with the best specifications as a mass-produced product.
Thorough quality control is carried out in product manufacturing (assembling to the shipping state). First, carefully check the appearance and dimensions of the parts. Seal grooves, which are difficult to measure, are also inspected with a dedicated measuring instrument. It is also a show of craftsmanship to be careful not to affect the product by integrating the delicate tolerances of each component such as the caliper body, seal, and piston. We will assemble it carefully, perform final confirmation such as leak test, and deliver it to everyone.
|
|
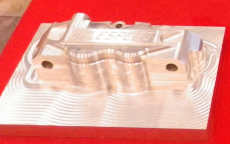 |
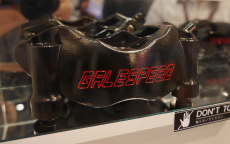 |
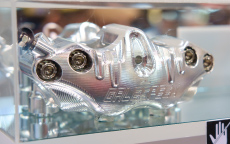 |
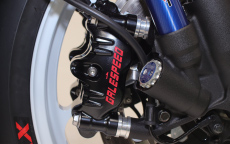 |
2014 |
2016 |
2017 |
2019(mass production) |
|
|